Washing the world of microplastics
These new solutions aim to catch plastic microfibres before they escape from your washing machine.
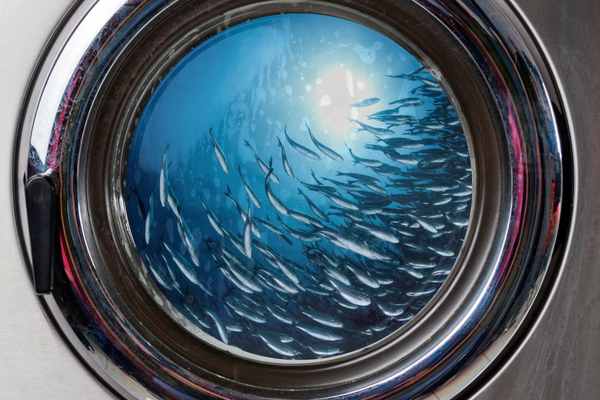
These new solutions aim to catch plastic microfibres before they escape from your washing machine.
Few of us realise that every time we wash our clothes, we unleash hundreds of thousands of microscopic plastic fibres into the ocean.
According to researchers, an average 6kg load of washing creates 700,000 plastic microfibres, and these end up in our food and drinking water, potentially impacting our health and our ecosystems. Now some startups are on the case, creating special filters that can be retrofitted to existing washing machines to catch these sneaky fibres at the source.
Planetcare
Slovenian startup PlanetCare is one of those to have developed a microfibre filter targeting microplastic reduction.
PlanetCare, which was founded by former Slovenian lawyer Mojca Zupan, created its first prototype in late 2017 and to date has developed domestic, commercial and industrial microfibre filters. Its patented filter tech uses mesh in a three-stage filtration process, similar to a car exhaust.
PlanetCare says its filters, which can be installed on washing machines in less than ten minutes, have been independently tested and shown to stop 90 per cent of microfibres.
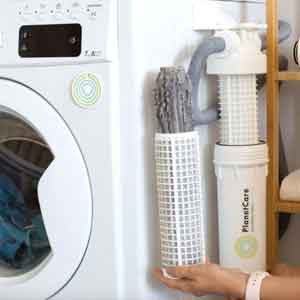
Each PlanetCare filter comes with reusable cartridges that can be replaced once full and sent back to the company to be refurbished for future use, with the caught fibres collected for recycling.
According to PlanetCare, the cartridges fill up with microfibers after about 15-20 washes. Replacing them only takes a few minutes, and users can make a one-time purchase or take out a subscription.
“Our vision is that in the future all washing machines will be equipped with efficient filters that will automatically stop fibres,” the company says.
PlanetCare, which was a finalist in The Ocean Impact Pitchfest 2022, says users of its technology could stop over 500 tons of microfibre emissions from entering into the wastewater in the next five years.
Gulp
Another filter maker preparing to enter the market is UK startup Matter, founded by a former Dyson mechanical engineer, Adam Root.
A year ago, Matter was awarded £150,000 from the British Design Fund to scale up its microplastics solutions, which include a microfibre washing machine filter called Gulp to be launched in July next year. The company has patented its filter, which does not need to be replaced.
The Gulp filter will work with all European-style washing machines and is also suitable for Australasia, with Gulp V2 under development for North America.
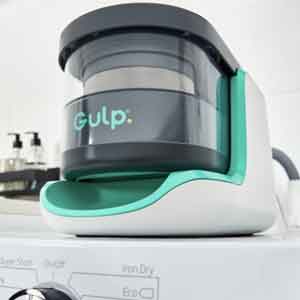
It can be placed above or at the side of each washing machine and will retail for around £250 (but advance orders are being accepted on Indiegogo for £179).
The Gulp filter can be emptied into the bin once the LED changes colour, but Matter also plans to recycle the plastic collected. The company says it will be accepting returns of captured microfibres next year. These will be used for ongoing research or recycled into new products.
“Recycling microplastic captured from our products is the next step, which is why we are leading a number of research projects using the microfibres sent to us to find sustainable solutions for recycling microfibres from our laundry,” Matter says.
“Findings from our latest research confirm the suitability of compressed microfibres as a replacement for insulation panels. Our mission is to continue R&D into the reuse of microfibres to find the most sustainable solutions possible.”
There are other ways to reduce microplastics pollution, say experts, including washing clothes at lower temperatures and washing only when necessary, and buying new clothes less often as new clothing has been found to shed more fibres.
These days, 60 per cent of clothes are made from synthetic fibres such as acrylic and polyester, so another solution is to buy clothes made from natural fibres such as cotton, wool and linen from sustainable sources.
NANOLLOSE
One startup with this ambition is Nanollose, an Australian publicly-listed startup that is creating a new type of non-shedding fabric from sustainable sources.
Nanollose has just created the first wearable garment – a sweater – using its eco-friendly ‘tree-free rayon’ fibre which it calls Nullarbor. It is sourced from sustainable coconut waste and is biodegradable.
Nullarbor is made by fermenting liquid waste products from food industries into cellulose, a cotton-like raw material in around 18 days in a production process that uses little land, water or energy.
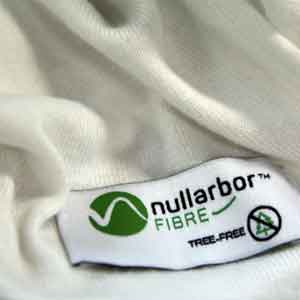
Traditionally, cellulose has been obtained from less sustainable tree-based sources such as cotton, flax and timber. These sources require considerable agricultural land and inputs, and take a long time to produce, putting pressure on natural resources.
Nanollose’s process in contrast uses industrial organic and agricultural waste. The company’s executive chairman Wayne Best recently said: “We have successfully taken waste and created clothing, and we have done it following industrial protocol.
“We didn’t have to cut down any trees to create this sweater, and we have now demonstrated that our ‘tree-free rayon’ fibre can be used in the same way as other commonly-used fibres to make clothing and textiles, without the hefty environmental footprint.”
According to Nanollose, its new fabric is now ready to move out of the laboratory and into the factory to provide an alternative eco-friendly option available to manufacturers at scale. To this end, the company recently signed an MOU with Zara’s parent company Inditex for testing and prototyping.