Cracking the concrete challenge
Substituting carbon-heavy cement with waste ingredients is a key focus for innovators in the sector.
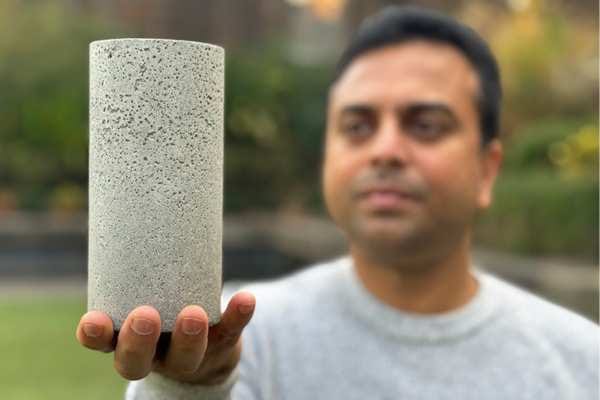
As the construction sector confronts one of its most stubborn carbon challenges, a wave of new innovations could reshape the concrete supply chain.
Concrete is one of the most widely used materials on Earth, and one of its key binding ingredients – cement – is also among the most emissions-intensive. According to the World Economic Forum, cement manufacturing accounts for about 8 per cent of the world’s total carbon dioxide emissions.
Most of these emissions are released during the chemical conversion of limestone into calcium oxide, a process that occurs at high temperatures and is intrinsic to cement production. As a result, this cannot be fully addressed by switching to renewable energy, making cement particularly difficult to decarbonise.
New approaches that seek to replace cement with alternative materials, often from waste streams, are stepping in. One area attracting growing interest is geopolymer concrete, a class of material that offers lower embodied carbon compared with traditional cement-based concrete.
"Concrete is an essential building material, but cement remains one of the largest contributors to man-made carbon emissions."
Instead of using cement, geopolymer concrete is made by activating industrial waste products such as fly ash and blast furnace slag. Although a number of trials and early commercial projects have shown promise, experts say barriers to more widespread adoption centre around the need for national codes and standards specific to alternative concrete mixes.
One Australian company with a commercially available geopolymer concrete is Queensland-based construction materials company Wagners. Its Earth Friendly Concrete has been used in projects including airports, buildings and local road infrastructure.
"Concrete is an essential building material, but cement remains one of the largest contributors to man-made carbon emissions. By removing 100% of the cement content, Earth Friendly Concrete reduces 70% of the CO2 associated with concrete," the company says.
Cement substitutes
Other efforts to decarbonise concrete production take a more incremental approach by focusing on reducing the quantity of cement in concrete.
Engineers at RMIT University have developed a low-carbon concrete that they claim can recycle twice as much coal ash as current standards and halve the amount of cement required, while still providing strong performance over time.
A pilot computer modelling program developed by RMIT in partnership with Hokkaido University was used to forecast the time-dependent performance of its new concrete mixtures.
According to Dr Yuguo Yu, an expert in virtual computational mechanics at RMIT, a longstanding challenge has been to determine how newly developed materials stand the test of time.
“We’ve now created a physics-based model to predict how the low-carbon concrete will perform over time, which offers us opportunities to reverse engineer and optimise mixes from numerical insights,” Yu said.
Unlike standard practices that rely on high-grade fly ash, the RMIT team says it has found a way to incorporate lower-grade “pond ash” sourced from coal slurry storage ponds – an underused resource that poses long-term environmental risks. The researchers say this approach could help solve two major environmental issues at once.
"We’ve now created a physics-based model to predict how the low-carbon concrete will perform over time, which offers us opportunities to reverse engineer and optimise mixes from numerical insights."
According to RMIT, its modelling has shown how ultra-fine additives can accelerate early setting and enhance material density, helping to offset the slower reaction rates of pond and fly ash.
RMIT has also studied the application of other waste streams for the making of concrete, including substituting a proportion of river sand with used coffee grounds.
Elsewhere in the sector, global materials company Mapei recently launched a new range of additives, including one developed locally, aimed at helping concrete makers reduce the quantity of cement used in their process. According to Mapei, its new Mapecube admixture range allows manufacturers to increase the use of fly ash and slag and reduce the quantity of cement (to varying degrees) while still maintaining traditional quality and strength.
“The essence of this product line is to do more with less,” Mapei’s Australian general manager, Marco DeSantis said. “This offers savings in CO2 production and even in cost per cubic metre.”
Curing carbon
A fundamentally different approach to bringing sustainability to concrete production comes from CarbonCure Technologies. The Canadian company has developed a process that transforms the material into a storehouse for unwanted CO2 emissions captured from a range of industrial outputs. In this process, producers can inject carbon dioxide captured externally directly into fresh concrete for permanent storage.
The company has attracted strong backing from Breakthrough Energy Ventures – a fund founded and chaired by Bill Gates – as well as several prominent business leaders.
According to CarbonCure, carbon savings are achieved through both CO2 mineralisation (CO2 storage) and cement reductions with its technology that has already been used to remove more than 587,000 metric tonnes of CO2 across a range of production sites.
Cement is primarily made by heating limestone (calcium carbonate) and clay in a kiln at high temperatures (up to 1450°C) to produce clinker, which is then ground with gypsum to make cement. The process emits carbon dioxide (CO2) in two major ways. First, the intense heat required for the kiln which is generated by burning fossil fuels, releasing CO2. Second, CO2 is released through a chemical reaction called calcination. In this reaction, limestone decomposes into lime (calcium oxide) and CO2 gas. This calcination step accounts for around 60% of total cement-related emissions.